Initiative ouverte afin de promouvoir la M&SN et les technologies associées (Dispositifs Médicaux)
Publié le 16 mai 2023 08:35:00
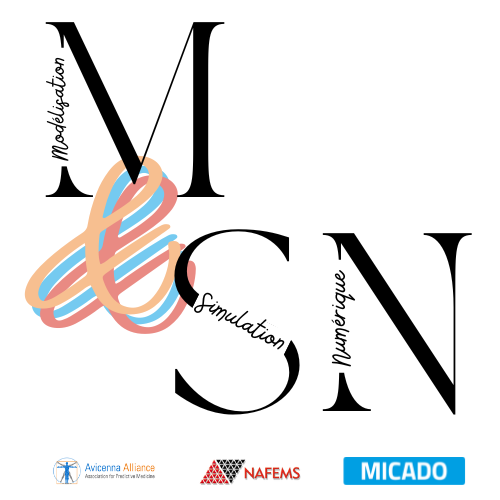
Si en France nombreux sont les praticiens et académiciens qui ont déjà adopté les nouvelles méthodes in-silico basées sur la modélisation et la simulation numérique (M&SN), les jumeaux numériques ou l’IA, il n’en est pas de même des fabricants français de dispositifs médicaux à l’exception de quelques entreprises pionnières et start-up.
C’est pourquoi devant l’urgence de la situation et le risque économique pour la filière à moyen terme, l'Alliance Avicenna, NAFEMS France et MICADO créent une initiative ouverte à tous les acteurs français ou francophones, afin de promouvoir la M&SN et technologies associées particulièrement auprès des fabricants de dispositifs médicaux en France.
Vous trouverez ci-dessous un projet de "Manifeste" et nous vous invitons à rejoindre le "Comité d'Orientation" qui validera un plan d'actions 2023 et au-delà.
La présentation virtuelle (Webex) de cette initiative aura lieu le mardi 13 juin prochain de 17h00 à 19h00.
Vous pouvez par avance réserver cette date dans vos agendas (invitation webex à venir).
Didier Large de NAFEMS France
Thierry Marchal, secrétaire général d'Alliance Avicenna
Daniel Fougères et Nicolas Gardan de l’association MICADO
Jean-Marc Crepel membre de NAFEMS et vice-président de MICADO

L’objectif de cet axe de recherche chez MICADO consiste à faire une évaluation des besoins, des méthodes et des points critiques dans une démarche de travail collaboratif comprenant la conception, la modélisation numérique et la simulation dans un contexte donneur d’ordres / sous-traitants.
Une méthodologie a été développée, basée sur la méthodologie PRO3 définie pendant ma thèse [1], [2], [3], [4], et le projet DIJA [5] [6]. Cette méthodologie, étendue à la méthodologie P4LM, permet de structurer la connaissance selon plusieurs niveaux d’abstractions (appelés en réalité environnements car chaque environnement peut lui-même avoir plusieurs niveaux d’abstractions).
La Figure 2 présente de manière globale l’architecture mise en place. Elle est principalement basée sur la modélisation par les processus, fondamentale dans le cadre de la mise en place d’un scénario de travail collaboratif [7] [8] [9] [10] [11] [12]. Le P4 de P4LM signifie la prise en compte des notions de Processus, de Projet, de Procédé et Produit :
- un projet est l’ensemble des actions à entreprendre afin de réaliser un objectif dans des délais impartis. Un projet est donc un objet temporaire impliquant des ressources humaines et matérielles définies et identifiables. Un projet contient des produits, des procédés, des processus, des intervenants, des contraintes et des connaissances.
- un processus représente une succession de tâches dont la mise en œuvre va contribuer à modifier le produit. Un processus peut représenter un processus de conception. Un processus est considéré comme un graphe de procédés. Il peut accepter en entrée (E) un ou plusieurs produits, et retourne en sortie un ou plusieurs produits (S). Il est éventuellement soumis à des contraintes (C), et accepte l’intervention d’intervenants qui peuvent accéder à un ensemble de connaissances (K) (voir Figure 2). Un processus est décrit par un graphe dont les nœuds sont des procédés et les arcs sont orientés et valués par une valeur normalisée (comprise entre 0 et 1) qui correspond au pourcentage de réalisation du produit (critère de qualité). Il est spécifié par des types de données d’entrée et des types de données de sortie. Si une entrée est également une sortie, il ne s’agit pas d’une entrée / sortie mais d’une production d’un nouveau produit (nouvelle version).
- un procédé représente les actions abstraites ou physiques qui vont entraîner la modification du produit. Un procédé peut représenter à un certain niveau d’abstraction un procédé de fabrication mais il peut également représenter à un niveau d’abstraction proche métier des caractéristiques de forme par exemple. Un procédé est soit un procédé de base (terminal), qui effectue l’action de transformation du produit (ou de production d’un produit), soit décrit par un processus (encapsulé, non terminal). Respectivement, un procédé est donc soit une tâche ou soit une action. Un procédé dispose d’entrées et de sorties. Il peut être contraint et dispose de certaines connaissances. Si le procédé est non terminal, il est décrit par un processus et représenté par un nom. Si le procédé est terminal, on utilisera un nom et une description. Il pourra être classifié en procédé :
- Virtuel, par exemple logiciel
- Physique, par exemple machine
- Méthodologique, par exemple visioconférence, validation, procédure …
- un produit correspond à des données, spécifiées par un type de données (exemple : CdC, prototype physique, DMU, Note de calcul, …). Un produit représente toute information permettant de caractériser le produit au sens du modèle. Le produit peut avoir une représentation différente selon son niveau d’abstraction. Par exemple, une bielle est un produit au sens physique à un niveau d’abstraction élevé mais elle va avoir une représentation topologique et géométrique à un niveau d’abstraction très bas. Un produit est spécifié par un type (virtuel ou physique). Il est décliné en différentes versions, disposant chacune d’un critère de qualité et pouvant avoir des cycles de vie indépendants. Chaque produit peut être associé à des contraintes.
L’architecture multi niveaux [4] définit une hiérarchie fonctionnelle du produit en cours de conception. Ces niveaux sont des niveaux sémantiques car ils définissent des niveaux d’abstraction de la connaissance. Il y a cinq environnements qui peuvent contenir plusieurs niveaux d’abstraction (suivant le contexte) listés ici par ordre sémantique croissant :
- un environnement géométrique qui contient les informations permettant de créer des modèles géométriques. L’objectif est de couvrir un large spectre des applications possibles des modèles géométriques comme les CSG (Constructive Solid Geometry), un BRep (Boundary Representation) ou encore un maillage par éléments finis.
- un environnement dialogue qui est relatif dans le projet DIJA aux éléments de dialogue. Dans les systèmes de CAO actuels, un utilisateur modifie le modèle CAO en agissant sur les features ou directement sur les faces, les points ou les courbes, … Or un utilisateur novice peut difficilement s’approprier ce genre d’outil. C’est pour cette raison que les éléments de dialogue ont été définis pour permettre à un utilisateur novice de concevoir un modèle CAO de manière synthétique et non plus constructive. C’est une approche très intéressante notamment pour la fabrication additive.
- un environnement commun qui contient les informations communes à tous les métiers. Ce niveau dit intermédiaire permet de gérer les notions générales communes à tous les métiers. C’est par exemple à ce niveau que sont contenues les règles concernant les différents matériaux enregistrés dans le module de connaissances (loi de comportement du matériau et caractéristiques par exemple).
- un environnement métier qui permet d’associer les informations à un métier spécifique. C’est dans ce niveau que chaque règle ou scénario spécifique au domaine est enregistré.
- un environnement collaboratif qui est le niveau d’abstraction le plus élevé. Il permet de définir au départ les processus collaboratifs permettant de structurer le projet et la connaissance.
Cette méthodologie est supportée d’un point de vue logiciel par un outil de modélisation développé en interne basé sur une approche client serveur. Il permet de décrire une problématique par une modélisation par les processus. Chaque procédé répond à la démarche P4LM en ayant la possibilité d’associer des documents divers (images, vidéos, …), des tableurs de calcul, et d’exécuter des programmes sur le cloud (lancement de maillages en batch Hypermesh, calculs linéaires / non linéaires sur Code-Aster, …). Un procédé peut être associé à un outil de visualisation / analyse 3D pour des modèles 3D, des modèles éléments finis et du G-Code pour la fabrication additive. Cet outil central dans la démarche MICADO est utilisé pour le projet CertifIngenum© pour l’autoévaluation de compétences et la formation des ingénieurs en simulation numérique de tenue mécanique et technicien en fabrication additive polymère.
Bibliographie
1 - (NGardan, 2003-a) N. Gardan, « Modélisation automatique de systèmes de remplissage en fonderie moulage sable sur Internet – Automatic modelling of sand casting filling systems on the Internet », Rev. Fonderie Fondeur Drqaujourdrqhui Rubr. Rech. Res., no 229, p. 26–35, 2003.
2 - (NGardan, 2003-b) N. Gardan et Y. Gardan, « An application of knowledge based modelling using scripts », Expert Syst. Appl., vol. 25, no 4, p. 555‑568, 2003, doi: 10.1016/S0957-4174(03)00096-4.
3 - (NGardan, 2004) N. Gardan et R. Maranzana, « Méthodologie de travail collaboratif autour de la chaîne numérique », Paris, 2004.
4 - (NGardan, 2005-a) N. Gardan, « Proposition d’une méthodologie de travail collaboratif : Concepts et applications », Université de Reims Champagne-Ardenne, 2005.
4 - (NGardan, 2005-b) Nicolas Gardan, Y Gardan « A methodology for co-design: concepts and applications » The 2005 International Conference on Modeling, Simulation and Visualization Methods-MSV, Las Vegas
5 - (Danesi & al, 2003) F. Danesi, N. Gardan, Y. Gardan, et E. Perrin, « Synthetic Modelling System Architecture », Proc. Int. Conf. Geom. Model. Graph. GMAG03, p. 174–180, juill. 2003.
6 - (YGardan & al, 2002) Y. Gardan et al., « First operational systems based on the dija project », in IASTED international conference on applied modelling and simulation (AMS 2002), 2002, p. 294–299.
7 - (Danesi & al, 2006) F. Danesi, N. Gardan, et Y. Gardan, « Collaborative Design: from concept to application », Int. Conf. Geom. Model. Imaging 2006 GMAI2006, juill. 2006.
8 - (Danesi & al, 2008) F. Danesi, N. Gardan, Y. Gardan, et M. Reimeringer, « P4LM: A methodology for product lifecycle management », Comput. Ind., vol. 59, no 2–3, p. 304‑317, 2008, doi: 10.1016/j.compind.2007.06.013.
9 - (Danesi & al, 2012-a) F. Danesi, N. Gardan, et E. Kwassi, « Knowledge Based Engineering Optimization and Interoperability: An Automotive Case-Study », Appl. Mech. Mater., vol. 232, p. 823–827, 2012.
10 - (Danesi & al, 2012-b) F. Danesi, N. Gardan, E. Kwassi, et M. Reimeringer, « Design Process Automation and Optimization using industrial knowledge based Simulation and Design », in 23rd IASTED International Conference on Modelling and Simulation, Banff, Canada, 2012, vol. 232, p. 823–827.
11 - (NGardan & al, 2003-c) N. Gardan et Y. Gardan, « A web-based system using trade knowledge », in Geometric Modeling and Graphics, 2003. Proceedings. 2003 International Conference on, Londres, 2003, p. 22–27.
12 - (NGardan & al, 2003-d) N. Gardan, « Une méthodologie de travail collaboratif donneur d’ordre/sous-traitant », Rev. Int. CFAO Inform. Graph., vol. 18, no 4, p. 467–484, 2003.

L’impression 3D est composée d’un ensemble de différentes technologies de fabrication qui ont comme point commun de créer une modèle physique couche par couche. A ce jour, 7 technologies d’impression 3D sont reconnues. Parmi ces technologies, la plus répandue est l’extrusion de matière, elle existe avec du filament polymère mais aussi avec du filament métal.
L’impression 3D métal peut être mise en œuvre sous différents procédés comme la fusion sur lit de poudre, le jet de liant, le dépôt sous énergie concentrée ou encore l’extrusion de métal. Le procédé présenté dans cet article fait appel à ce dernier, mais la matière n’est pas stockée sous forme de filament.
Le procédé BMD pour « Bound Metal Deposition » a été développé par la société Desktop Metal (Etats-Unis). Basé sur l’exploitation des poudres MIM (Metal Injection Molding) ce procédé est similaire à un procédé de type FFF (Fused Filament Fabrication), la seule différence est la manière dont est stockée la matière. Pour un procédé FFF la matière est sous forme de filament alors que pour la technologie BMD la matière est sous la forme d’un bâton composé de poudre métallique et d’un liant servant d’agglomérant.
A ce jour les matières disponibles vont des aciers inox 17-4 PH et 316 L, à des aciers H13 ou 4140, en passant par le cuivre (Cu) ou le titane (Ti 64).
Préparation à l’impression
Dans la même optique que des pièces polymères imprimées avec une technologie FDM, il est possible de paramétrer le remplissage en choisissant entre un remplissage de type lattice gyroïde ou une pièce pleine. Comme pour d’autres procédés d’impression, des supports peuvent être nécessaires. Avec la technologie BMD les supports s’impriment dans la même matière que la pièce, mais sont séparés de celle-ci par une fine couche de céramique qui brûle lors de l’étape de déliantage. Cela permet de séparer les supports de la pièce sans outils et sans risques de dégrader l’aspect de surface.
Processus d’impression
La matière est extrudée par l’intermédiaire d’une buse chauffée à 165°C, celle-ci est déposée couche par couche sur un plateau chauffant. L’intérieur de la chambre d‘impression est lui aussi chauffé avec une température proche des 50°C. En fonction des paramètres d’impression les couches varient de 0,05 mm pour les impressions de haute précision, jusqu’à 0,3 mm pour des impressions de qualité standard.
A la fin de l’impression, la pièce qui en résulte s’appelle « verte ». Cette pièce est en moyenne 18% plus grosse que la pièce finale. A cette étape, la pièce a des propriétés mécaniques relativement faibles. On pourrait comparer cette pièce verte à une pièce en plasticine très peu malléable.
La prochaine étape consiste à retirer le liant présent avec la poudre métallique, cette étape s’appelle le déliantage thermique. Elle se réalise en plaçant la pièce dans un four, qui va monter à un premier palier de température. A ce stade, le liant est brûlé. Il ne reste plus que les particules de métal.
La dernière étape consiste à « fritter » ces particules de métal entre elles. Pour cela, le four monte à un deuxième palier de température, compris entre 1200 et 1400°C. Les pièces sortent du four avec une densité allant jusqu’à 98%, ce qui est similaire à des pièces de fonderie.
Les avantages du BMD
L’avantage majeur de la BMD face au SLM (Selective Laser Melting) est le fait que l’on ne travaille pas directement avec les poudres de métal. Les poudres sont agglomérées avec le liant dans le bâton. Les particules de poudre métallique sont très volatiles et peuvent être respirées par les opérateurs qui les manipulent. Il est donc impératif de porter des EPI (Equipement de protection individuelle), comme des masques pour éviter d’en inhaler.
Le coût d’une solution de frittage laser est souvent 3x plus élevé qu’une machine d’impression BMD.
Post-traitement des pièces BMD
Plusieurs solutions de post-traitements sont disponibles sur les pièces, comme du sablage ou un ponçage de pièce verte. Une tribofinition est réalisable, elle consiste à mettre la pièce dans un tambour vibrant rempli de grains de ponçage. Le résultat varie selon le média utilisé. La dernière solution de post-traitement est l’usinage. En effet, il est possible de venir usiner les surfaces fonctionnelles d’une pièce en post-impression. Cela permet d’obtenir des alésages ou surfaces d’une excellente précision.
La plateforme de Fabrication Additive Technopolis bénéficie de l'expertise MICADO pour la mise en place et l'utilisation de cette technique dans les Alpes-de-Haute-Provence.
De l’intérêt pour l’ingénieur de ne pas utiliser inconsidérément les tableurs
Publié le 10 janv. 2023 11:00:00

L’intégration de l’utilisation des tableurs comme par exemple Excel dans les entreprises s’est principalement effectuée grâce à leur coût très faible et leur facilité d’utilisation. Ils peuvent être sources d’erreurs catastrophiques, notamment dans les domaines de l’ingénierie, où ils sont largement utilisés pour des tâches diverses et variées : création de modèles de calculs internes, suivi de projet, suivi de stocks matières, calcul de devis, ...
Les tableurs sont très utilisés dans les équipes projets comme points d’entrées à de nombreuses décisions. Un tableur est souvent le premier outil que les ingénieurs ou les scientifiques ont en main lorsqu’ils traitent des données numériques. Le diagnostic des incohérences est certainement la plus grosse contrainte de ces outils : il est presque impossible, vue la difficulté d’interprétation et de lecture des formules, de pouvoir valider le fonctionnement de feuilles de calculs de tableurs. Il est par exemple très difficile de pouvoir contrôler les unités des valeurs calculées, des erreurs peuvent ainsi s’insérer dans les tableurs contenant de nombreuses cellules. Il est nécessaire de réaliser des audits souvent lourds pour s’assurer de la validité du modèle.
La majorité des feuilles créées n’utilise pas la possibilité offerte généralement par ces outils de renommer les cellules pour rendre les formules plus lisibles, tant la fonction pour renommer est lourde à utiliser. De manière générale, l’approche "objet" est inexistante, ce qui rend les feuilles de calculs très instables :
• une quantité de données trop importantes est très difficile à gérer et rend l’approche qualité et la validation des résultats difficiles à mettre en oeuvre,
• l’utilisation du copié-collé, pratique courante, est une source d’erreur évidente (décalage des références, prise en compte de mauvaises valeurs, ...),
• la gestion des références croisées sur la base de données qui sont souvent dupliquées est très problématique. Il n’est pas assuré que la mise à jour après la modification d’une cellule soit correctement répercutée sur l’ensemble des feuilles.
La traçabilité des différentes modifications, si importante dans la gestion de projet, est presque impossible à mettre en place. Il est ainsi très difficile de sécuriser efficacement tout ou partie d’une feuille de calcul. La possibilité d’automatiser des sous-ensembles de calcul est loin d’être évidente, à part en utilisant des scripts dont la pérennité est difficile à maîtriser.
Un groupe de travail européen a été créé sur la gestion des erreurs de feuilles de calcul. Ce groupe, appelé EuSpRig (eusprig.com), a pour mission de publier les bonnes pratiques et les informations sur l’état actuel de la gestion des risques liés à l’utilisation de tableurs. Une conférence est organisée tous les ans permettant de faire le point sur des études de cas d’assurance qualité, de la gestion des risques, des bonnes pratiques, des problématiques liées aux facteurs humains et psychologiques, de la maintenance continue et l’assistance aux utilisations, de la surveillance de l’utilisation des grandes feuilles de calcul, ...
La section « Horror Stories » disponible sur le site recense quelques perles de la mauvaise utilisation de tableurs
Il est certain qu’une erreur humaine peut s'insérer dans n’importe quel système informatique, mais les systèmes de type tableurs y sont particulièrement sensibles. Selon (Panko, 2005), 88% des feuilles de calcul contiennent des erreurs. Selon le rapport (IDC, 2017) environ 55 milliards d’euros par an sont gaspillés en Europe en raison de la répétition d’erreurs dans les feuilles de calcul. Chaque utilisateur de feuille avancée peut passer jusqu’à 9 heures par semaine d’efforts répétés pour mettre à jour les sources de données, une dépense de 10 000 euros par an en moyenne par utilisateur.
Dans le cadre des accompagnements de MICADO auprès des PME / TPE pour des projets pilotes en ingénierie numérique, nous avons pu constater la presque hégémonie de l’utilisation des feuilles de calcul type Excel pour les modèles mécaniques, matériaux, ... Certaines feuilles de calcul sont ainsi très avancées et contiennent une modélisation de la connaissance de l’entreprise très poussée. Par contre, les ERP ont très majoritairement remplacé les feuilles de calcul pour la gestion des projets, de la comptabilité, de la gestion des risques et la conformité, ...
Nous avons pu constater que dans les TPE la gestion de suivi de projet est encore traitée sur des feuilles de calcul type Excel, avec des lignes interminables de tâches à réaliser, impossibles à tenir à jour. Ces tableurs appelés SdP (Suivi de Projet) sont en plus souvent reliés à des feuilles de calculs permettant de déterminer des valeurs à des données techniques. Il est également très courant dans les projet TPE / PME d’avoir de nombreux fichiers de calcul de type Excel reliés entre eux, dont il est très facile de rompre des liens en réalisant des copiés-collés.
Il n’est pas question ici de tirer à boulets rouges sur un outil très pratique tant que le nombre de données reste limité. Mais dès qu’une feuille de calcul contient de trop nombreuses données, des données croisées, de nombreuses formules, ... il est absolument nécessaire de mettre en place une nouvelle démarche. Cela peut être l’utilisation de bonnes pratiques ou des programmes permettant de créer des bases de données sur la base des feuilles de calculs (comme par exemple PowerPivot pour Excel). Mais le plus intéressant est d’utiliser des systèmes informatiques permettant de gérer la traçabilité des données et leur unicité au travers d’une plateforme collaborative unifiée. De nombreux outils sont disponibles sur le marché. Ils permettent d’automatiser les étapes d’analyse grâce à des processus, intègrent des algorithmes de Machine Learning pour des analyses poussées, ...
Il serait intéressant d’avoir sur le marché un outil aussi simple d’utilisation qu’un tableur tel qu’Excel permettant de lever les contraintes sources d’erreurs précisées plus haut, avec la possibilité de créer des processus.
Sources :
- Avis d’expert Usine nouvelle, 2020, Excel est il toujours incontournable ? https:// www.usinenouvelle.com/article/avis-d-expert-excel-est-il-toujours-un-incontournable.N1017549
- (Panko, 2005) R.R. Panko « What we know about spreadsheet errors » Journal of organizational and end user computing, 2005
- (IDC, 2017) « The state of self-service data preparation and analysis using spreadsheets in Europe », An IDC InfoBrief, commissioned by altered, 2017
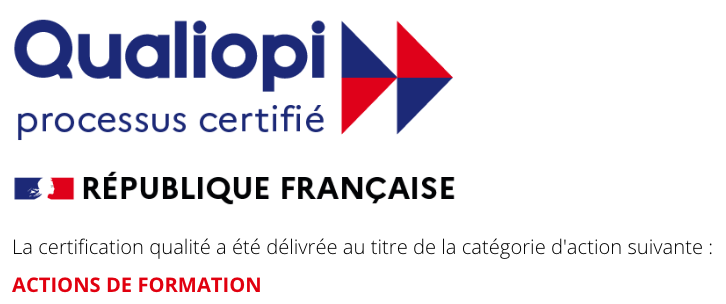
Nouveauté 2023 !
MICADO vous accompagne pour la mise en place de vos formations.
Grâce à sa certification Qualiopi, MICADO-Académie est en mesure de vous épauler pour vos formations. A travers une prestation de service, MICADO vous propose un suivi sur l'ensemble du processus de formation, depuis le diagnostic préalable à l'entrée en formation jusqu'à l'attestation de réussite du stagiaire. MICADO endosse alors la responsabilité de la qualité comme indiqué dans la certification Qualiopi, en mettant en place les modalités qui assurent la chaîne de la qualité avec les sous-traitants.
Vous pouvez choisir de faire appel à nos experts-formateurs certifiés MICADO ou à l'un de vos formateurs habituels, qui devra être certifié MICADO afin de répondre à la charte établie par MICADO-Académie.
Vous pouvez d'ores-et-déjà demander un devis à communication@afmicado.com (tarif privilégié pour les adhérents/abonnés MICADO).